你不知道轮毂螺栓断裂的二三事
1.概述
现有轮毂螺栓断裂残件2件,完好件4件,等级为10.9级,材质为SCM435,螺母三件,安装于车辆轮毂处,服役过程中失效,要求分析失效原因。图1~4所示为试样宏观形貌,螺栓断裂位置为螺纹收尾处,断口及断口附近均未见明显的塑性变形,断面内部分区域存在磨损痕迹。螺母中(图3所示),两件表面磨损严重(图3所示1、2号样),一件表面轻微磨损(图3所示3号样),检测螺母螺纹,发现1号螺母约1/2的内螺纹已经严重磨损(图4红色虚线所示)。
图1 试样宏观形貌
图2 试样宏观形貌
图3 试样宏观形貌
图4 试样宏观形貌
2.断口分析
任取一件失效件进行断口扫描,图5所示为2号失效螺栓断口的宏观形貌,断面较平整,断口附近无明显塑性变形;断口边缘可见轮辐状台阶,断面内可见明显的“贝纹线”,由左、右、下侧边缘向中心扩展(图5红色箭头所示)。将断口分为A、B、C、D四个区域进一步描述。
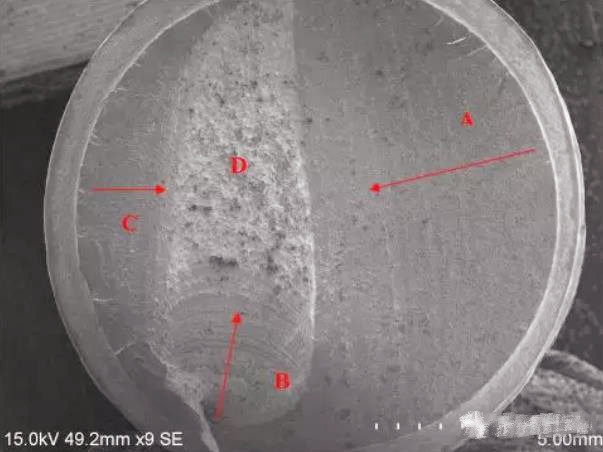
图5 1号失效螺栓断口宏观形貌
图6~8所示为A区形貌,可见该区断口靠近边缘(A1区)存在轮辐状台阶,微观可见磨损痕迹,靠近芯部(A2区)可见疲劳辉纹。
图6 断面A区形貌
图7 断面A1区形貌
图8 断面A2区形貌
图9~11所示为B区形貌,可见该区断口清晰的贝纹线,起源于断口边缘向中部扩展,靠近边缘部(B1区)可见磨损痕迹,靠近芯部(B2区)可见疲劳辉纹。
图9 断面B区形貌
图11 断面B2区形貌
图12~14所示为C区形貌,可见该区断口靠近边缘(C1区)可见轮辐状台阶,微观下可见磨损痕迹,靠近芯部(C2区)可见少量韧窝。
图12 断面C区形貌
图13 断面C1区形貌
图14 断面D区形貌
断面D区可见大量韧窝,为螺栓瞬断区,如图15、16所示。
图15 断面D区形貌
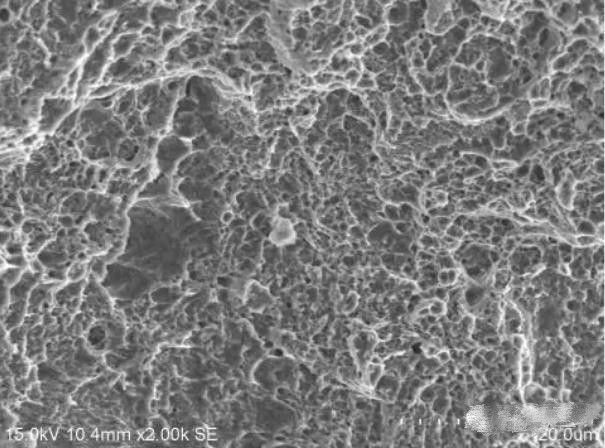
图16 断面D区微观形貌
3.金相检测
图17、18、19所示分别为1、2号断裂件和完好件芯部的金相组织,均为均匀的索氏体组织,无异常。
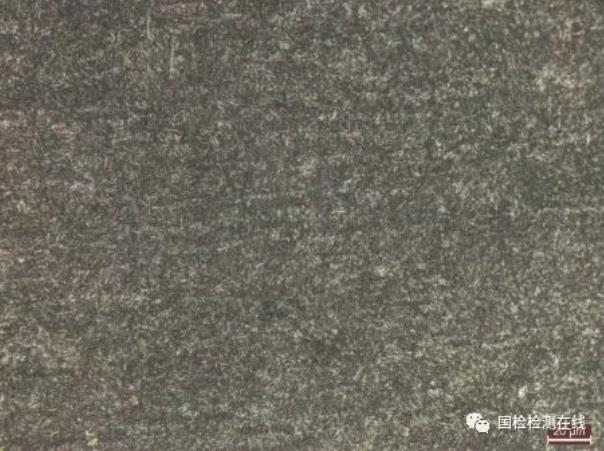
图17 1号断裂件芯部金相组织
图18 2号断裂件芯部金相组织
图19 完好件芯部金相组织
图20~22所示分别为1、2号断裂件和完好件的螺纹表面组织,未见表面不连续性缺陷。
图20 1号断裂件螺纹表面组织
图22 完好件螺纹表面组织
图23、24、25所示分别为断裂件和完好件的非金属夹杂物照片,根据“GB/T 10561-2005”标准可判定断裂件和完好件均为D类球状氧化物(细系)1级。
图23 1号断裂件非金属夹杂物
图24 2号断裂件非金属夹杂物
图25 完好件非金属夹杂物
4.性能检测
对螺栓进行脱(增)碳检测,结果如表1所示,根据“ISO 898-1:2013”中对10.9级螺栓的要求,可判定为螺栓断裂件与完好件均符合标准要求,断裂件与完好件的芯部硬度满足委技术要求(芯部硬度34-38HRC)。
表1 脱(增)试验结果(HV0.3)
表2 螺栓化学成分(%)
6.综合分析
螺栓断口形貌显示,宏观可见断面边缘存在轮辐状台阶,瞬断区位于接近断面中部位置,“贝纹线”清晰可见,分布瞬断区两侧,呈典型的多源疲劳断裂特征。通常情况下,紧固件疲劳失效的原因为:产品质量存在问题,装配工艺不合理,后期维护不到位等。
在本案例中,螺栓芯部金相组织、化学成分、洛氏硬度等指标均未发现明显异常。螺纹表面未发现脱碳现象或不连续性缺陷。另一方面,从工况上分析,轮毂螺栓在正常预紧状态下,主要受轴向拉伸载荷。但是,如果螺栓在安装时由于预紧力不一致,没有采取有效的防松措施,在服役时易发生松动而承受额外的剪切、弯曲载荷,导致其服役时在应力集中位置萌生疲劳裂纹。试样宏观形貌显示,其中一件螺母近1/2内螺纹严重磨损,表明螺栓失效前该组合件可能已发生松动。