分享:硅灰含量对碳毡/水泥复合材料摩擦学性能的影响
马少华1,费昺强1,周 松2,回 丽1
(沈阳航空航天大学 1.机电工程学院;2.航空制造工艺数字化国防重点实验室,沈阳 110136)
摘 要:采用扫描电镜分析和疲劳试验等方法,研究了腐蚀预损伤和盐水环境对7XXX 铝合金细节疲劳性能的影响,并探讨了对疲劳裂纹萌生和扩展的影响机理.结果表明:腐蚀预损伤和盐水环境对7XXX铝合金细节疲劳性能的影响较为显著;以未腐蚀试样在实验室空气环境下的细节疲劳额定强度截止值为基准,预腐蚀48h试样在实验室空气环境下的细节疲劳额定强度截止值的保持率为97%,未腐蚀试样和预腐蚀48h试样在盐水环境下的细节疲劳额定强度截止值的保持率分别为73%和67%.
关键词:铝合金;腐蚀预损伤;盐水环境;细节疲劳额定强度截止值
中图分类号:O346;V216 文献标志码:A 文章编号:1000G3738(2017)05G0063G05
InfluenceofPreGcorrosionDamageandSalineEnvironmenton
DetailFatiguePropertyofAluminumAlloy
MAShaohua1,FEIBingqiang
1,ZHOUSong
2,HUILi1
(1.CollegeofElectromechanicalEngineering;2.KeyLaboratoryofFundamentalScienceforNationalDefenseof
AeronauticalDigitalManufacturingProcess,ShenyangAerospaceUniversity,Shenyang110136,China)
Abstract:TheeffectsofpreGcorrosiondamageandsalineenvironmentonthedetailfatiguepropertyof7XXX
aluminumalloywereinvestigatedbySEManalysisandfatiguetests.InfluencemechanismofpreGcorrosiondamage
andsalineenvironmentontheinitiationandpropagationoffatiguecrackwasalsodiscussed.Theresultsshowthat
preGcorrosiondamageandsalineenvironmenthadsignificanteffectsonthe detailfatigue property of7XXX
aluminumalloy.Thedetailfatigueratingcutoffvalueforuncorrodedsampletestedinlabairwaschosenasa
benchmark,thedetailfatigueratingcutoffvalueretentionratesfor48hpreGcorrodedsampleinlabair,uncorroded
sampleinsalineenvironmentand48hpreGcorrodedsampleinsalineenvironmentwere97%,73% and67%,
respectively.
Keywords:aluminumalloy;preGcorrosiondamage;salineenvironment;detailfatigueratingcutoffvalue
0 引 言
民用飞机耐久性设计广泛采用的细节疲劳额定值(DFR)方法是在20世纪80年代由美国波音公司提出的,经 过 不 断 发 展 成 为 一 种 快 速 疲 劳 分 析 方法[1G2].细节疲劳额定值是指在应力比 R 为0.06、置信度为95%、可靠度为95%的条件下,结构能承受105 周次循环所对应的最大名义应力值(疲劳强度),其上限称为细节疲劳强度截止值,下限为结构允许使用的最小细节疲劳强度值[3G4].细节疲劳额定值主要用于评定结构以及其所采用材料的抗疲劳能力,不受载荷变化的影响,因此该值是评价材料固有疲劳特征与结构固有疲劳特征的重要参数.也正是由于此原因使得细节疲劳额定值方法成为评估细节疲劳寿命最行之有效的方法之一,并逐渐获得了民机疲劳寿命和耐久性设计人员的青睐[5].
飞机经常在雨水、盐雾、海水、潮湿空气等腐蚀性环境 和 交 变 载 荷 共 同 作 用 的 “复 合 环 境”下 使用[6].腐蚀损伤是飞机结构在整个服役阶段损伤的主要模式,随着飞机的老龄化,腐蚀损伤对飞行安全的威胁越来越大[7].飞机结构的使用寿命主要取决于结构质量和使用条件(载荷和使用环境),而细节疲劳性能决定了结构质量.因此,对不同环境下飞机结构的细节疲劳性能进行研究具有重要的工程实际意义.
近年来,国内外的众多学者在铝合金腐蚀预损伤、腐蚀疲劳和结构细节疲劳性能等方面进行了许多研究,但都是单独对某一方面进行研究,将两者结合起来研究得还比较少.陈先民等[8]为了将细节疲劳额定值法应用于含多相似疲劳细节结构的疲劳分析,依据细节疲劳额定值法和系统可靠性模型,建立了含多相似疲劳细节结构的细节疲劳额定值估算模型.康青山等[9]对2A12GT4铝合金进行了加速环境试验,并通过疲劳试验计算得到了细节疲劳额定强度,得到了其与停放时间的函数关系式.在腐蚀预损伤和腐蚀疲劳方面,张有宏[10]对 LY12CZ铝合金进行了 预 腐 蚀 后 的 疲 劳 和 腐 蚀 疲 劳 试 验,得 出SGN 曲线,初步建立了腐蚀损伤与疲劳寿命降低之间的关系.宫 玉 辉 等[11]研 究 了 不 同 腐 蚀 环 境 下7475GT7351铝合金的疲劳性能及疲劳裂纹扩展速率.KIMBERLI等[12G14]对 2024 铝合金及 7075 铝合金的腐蚀损伤及疲劳寿命预测进行了研究.作者分别在实验室空气和盐水环境中,对未腐蚀和预腐蚀48h的7XXX 铝合金试样进行了疲劳试验,研究了腐蚀预损伤和盐水环境对铝合金细节疲劳性能的影响.
1 试样制备与试验方法
将7XXX铝合金加工成细节疲劳额定强度截止值试样,沿轧制方向取样.7XXX 铝合金的化学成分见表1.按标准 HB7110-1994«金属材料细节疲劳额定强度截止值(DFRcutoff)试验方法»的要求进行预制损伤,一边用人工敲击制作,另一对角边用挫削制作,将加工好的试样等分成四组.试样的形状及尺寸如图1所示.对其中的两组试样进行预腐蚀处理,即将试样完全浸泡于丙酮中,超声清洗15min后放置于专用夹具上通风晾干,随后将其再浸泡于质量分数为3.5%的NaCl溶液中,48h后取出并去除表面的腐蚀产物,用去离子水清洗干净后吹干备用.
实验室空气环境的温度为(20±5)℃,相对湿度小于50%.盐水环境为采用 NaCl和去离子水配制而成的质量分数为3.5%的 NaCl溶液,试验时试样完全浸没于盐水溶液中,腐蚀装置内的溶液为连续循环,每周更换一次.按照金属材料细节疲劳额定强度截止值试验方法进行疲劳试验,实验室空气环境和盐水环境下的试验频率均为10 Hz,加载波形为正弦波.将未腐蚀试样和预腐蚀48h后的试样分别在盐水环境和实验室空气环境下进行应力比R 为0.06的疲劳试验.采用4级成组法确定试样的中值SGN 曲线,试样的数量满足由变异系数确定的最小试验个数,中值疲劳寿命区间为 1×104 ~5×105,置信度 满 足95%.若试样未在预制损伤部位断裂或断口上有明显的冶金缺陷或其他缺陷,则试验数据无效.
采用 NovaNanoSEM450型扫描电子显微镜(SEM)观察试样的疲劳断口形貌,分析腐蚀预损伤及盐水环境对7XXX铝合金细节疲劳性能的影响.
2 试验结果与讨论
2.1 疲劳性能
将未腐蚀试样和预腐蚀48h的试样在实验室空气环境和盐水环境下进行疲劳试验,试验结果如表2所示.参照 HB/Z112-1986«材料疲劳试验统计分析方法»对试验数据进行处理,用小子样数据估计母体参数,根据式(1)~(4)分别计算未腐蚀试样和预腐蚀48h试样在实验室空气环境和盐水环境下子样的平均值x- 、标准差S、子样变异系数Cv 和中值疲劳寿命 N50,结果列在表2中.
2.2 双点法求解细节疲劳额定强度截止值
根据式(5)和(6)求得置信度、可靠度均为95%的疲劳寿命 N95/95,结果列于表3中.分别将不同状态试样及不同试验环境下的 N95/95 画在纵、横坐标分别为最大应力和疲劳寿命的双对数坐标系上,连接相应两个 N95/95点的直线与寿命 N =105 交点的最大应力即是该条件下试样的细节疲劳额定强度截止值,如图2所示,求得的细节疲劳额定强度截止值见表3.
式中:β 为特征寿命;SR 为可靠度系数,SR =2.1;α为 Weibull分布函数的形状参数,对于铝合金α=4;R 为试验所要求的可靠度,R=95%;ST 为标准试样的试样系数,ST =1;SC 为置信度系数,通过查表4可获得。
从图2及表3中数据可以看出,腐蚀预损伤和盐水环境对铝合金细节疲劳额定强度截止值的影响较大,且盐水环境的影响更大.若以未腐蚀试样在实验室空气环境下的细节疲劳额定强度截止值为基准,则预腐蚀48h试样在实验室空气环境下的细节疲劳额定强度截止值的保持率为97%,未腐蚀试样在盐水环境下的细节疲劳额定强度截止值的保持率
为73%,预腐蚀48h试样在盐水环境下的细节疲劳额定强度截止值的保持率为67%.
2.3 腐蚀预损伤对铝合金疲劳寿命的影响
从图3中可以看出:在实验室空气环境和盐水环境下,预腐蚀48h试样的疲劳寿命均低于未腐蚀试样的疲劳寿命;与预腐蚀48h试样相比,未腐蚀试样的疲劳寿命数据更加分散.同一条曲线在低应力水平下的疲劳寿命数据比高应力水平下的疲劳寿命数据更加分散.腐蚀预损伤会在试样上留下腐蚀坑,腐蚀坑处的局部应力急剧升高,在疲劳载荷作用下,预腐蚀处的应力集中效应加强,裂纹快速萌生,使得裂纹萌生阶段占疲劳寿命的比例减少,因此疲劳性能下
降,疲劳寿命数据更加集中[16].
图3 实验室空气环境和盐水环境下腐蚀预损伤对7XXX
铝合金疲劳SGN 曲线的影响
Fig.3 InfluenceofpreGcorrosiondamageonSGN curvesof7XXX
aluminumalloyinlabair a andsalineenvironment b
2.4 盐水环境对铝合金疲劳寿命的影响
从图4中可以看出:未腐蚀试样和预腐蚀48h试样在盐水环境下的疲劳寿命明显低于实验室空气环境下的疲劳寿命,且在低应力幅值时这种差距更明显;对于未腐蚀和预腐蚀48h试样,在实验室空气环境下的疲劳寿命数据较盐水环境下的更加分散.盐水环境有效地助长了裂纹的起裂和扩展.在裂纹起裂阶段,盐水腐蚀造成试样表面损伤,疲劳裂纹起裂得更快;盐水环境对裂纹扩展的加速作用是
由裂纹扩展和盐水腐蚀过程的交互作用造成的,盐水进入裂纹尖端加速了裂纹扩展.因此,盐水环境对铝合金疲劳性能的影响更为显著.
2.5 疲劳断口形貌
盐水环境下产生的腐蚀坑使试样的应力集中效应得到了加强,疲劳裂纹源在腐蚀坑底部萌生,大幅缩短了裂纹萌生的时间,缩了裂纹萌生寿命;在疲劳和盐水腐蚀的交互作用下,裂纹尖端的循环滑移和破坏机制(解聚)使得裂纹加速扩展,所以7XXX铝合金在盐水环境下的疲劳性能大幅下降.
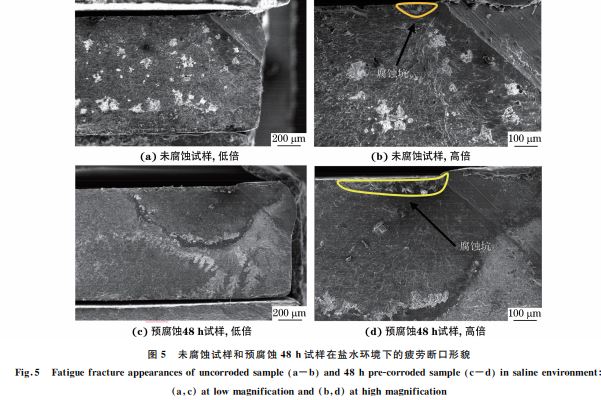
3 结 论
(1)腐蚀预损伤及盐水环境对7XXX铝合金细节疲劳性能的影响较为显著;以未腐蚀试样在实验室空气环境下的细节疲劳额定强度截止值为基准,预腐蚀48h试样在实验室空气环境下的细节疲劳额定强度截止值的保持率为97%,未腐蚀试样在盐水环境下的细节疲劳额定强度截止值的保持率为73%,预腐蚀48h试样在盐水环境下的细节疲劳额定强度截止值的保持率为67%.
(2)在实验室空气环境和盐水环境下,预腐蚀48h试样的疲劳寿命均低于未腐蚀试样的疲劳寿命,且未腐蚀试样的疲劳寿命数据相对分散.
(3)未腐蚀和预腐蚀48h试样在盐水环境下的疲劳寿命明显低于在实验室空气环境下的疲劳寿命,且在低应力幅值时这种差距更加明显,实验室空气环境下的疲劳寿命数据较盐水环境下的更加分散.
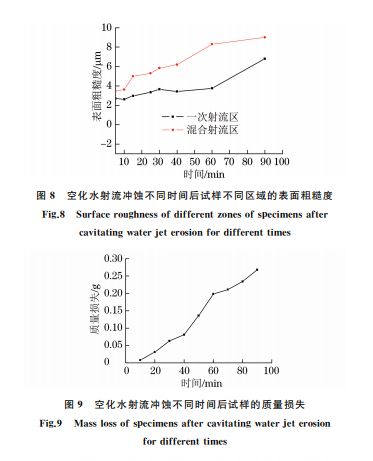
3 结 论
(1)一次射流区空蚀坑底部的晶粒弯曲变形,而混合射流区的截面组织无明显变化.
(2)在一次射流区,随空化水射流冲蚀时间的延长,纯铜表面的空蚀坑和空蚀针孔数量增多,晶粒形貌开始显现,同时出现大量的变形滑移带;混合射流区在短时间内出现大而浅的空蚀坑,且空蚀坑底部观察到晶粒形貌,随着时间延长整个混合射流区的晶粒形貌全部显现;空蚀坑是以空蚀针孔聚集导致少量金属剥落这种形式长大的.
(3)随空化水射流冲蚀时间的延长,一次射流区和混合射流区的表面粗糙度均逐渐增大,且混合射流区的表面粗糙度大于一次射流区的.
(4)混合射流区的硬化层厚度和近表层硬度均比一次射流区的大,硬化层厚度达到700μm.