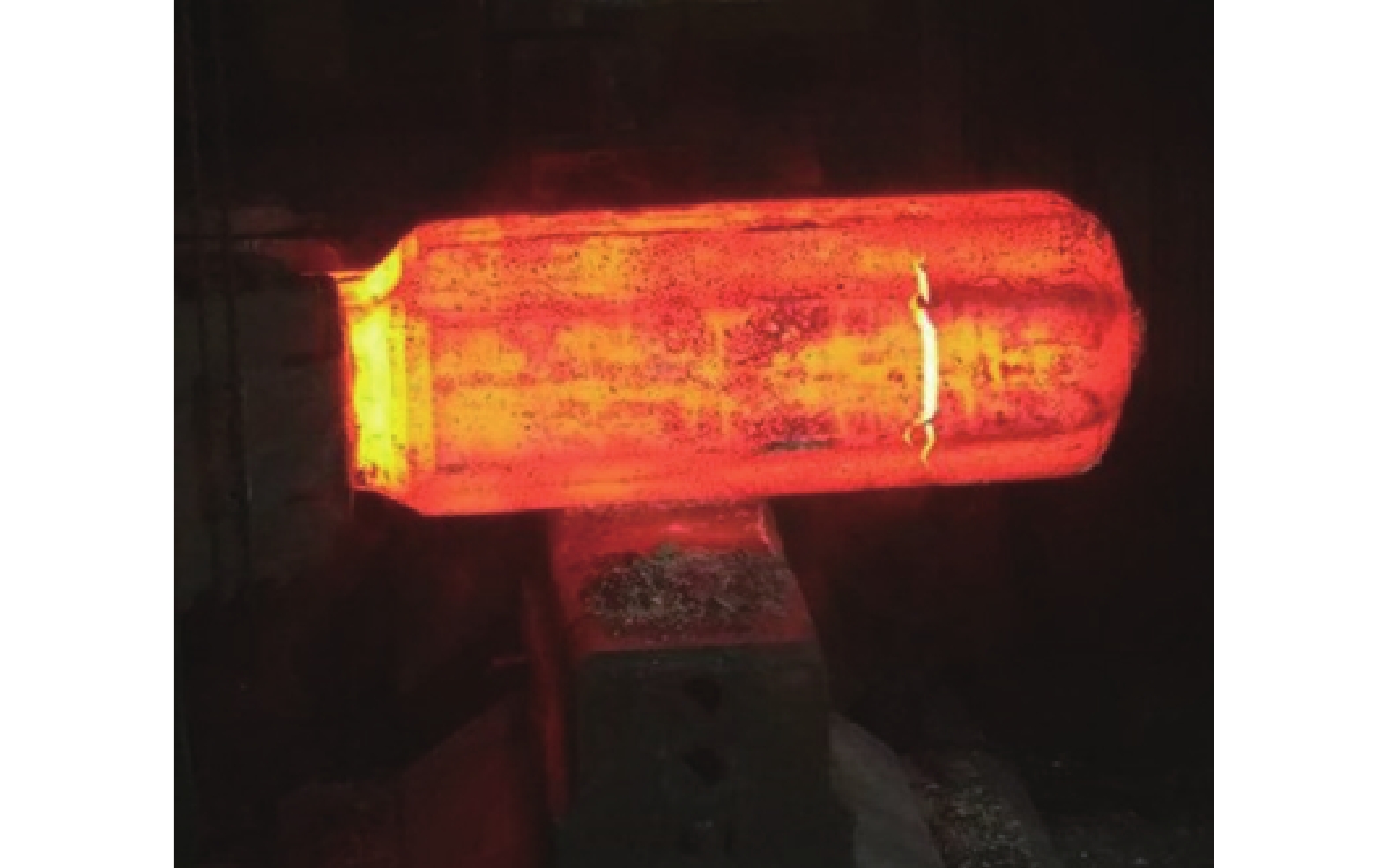
分享:钢锻制棒材探伤不合的原因分析和工艺改进
1.4112钢中含较高C、Cr,所以具有较高的淬透性和很好的耐磨性[1],因而被广泛地应用于恶劣环境中。由于含碳量高,韧性较低,易脆性断裂[2]。在我国,该钢曾作为航天航空尖端材料进行研制。近年来,随着该钢种在不锈、轴承、刀具行业的推广应用[3],国内的特钢企业进行过少量生产,多用于制造受冲击负荷较小的零件或工具[4]。由于1.4112钢属高碳马氏体型不锈钢,与中低碳马氏体不锈钢相比,塑性较差,可锻温度区间较窄[5],且生产时极易出现碳化物开裂,使钢材不得不判废或改锻。2017年改变加热介质以来,探伤合格率一直处于波动的状态,比之前有较大的下滑。近期一度降到47%且发现有肉眼可见的孔洞,严重影响了公司的合同交付率。因此,提高探伤合格率成为本文的主要研究方向。
1. 生产工艺流程和设备参数
1.1 生产工艺流程
根据成材规格,制定1.4112钢生产工艺流程:
(1)冶炼→模铸→1000 t精锻成材(简称1000直材)或1800 t快锻+1000 t精锻成材(简称1800+1000联合材),生产≤?120 mm削皮材。
(2)冶炼→模铸→1800 t精锻成材(简称1800直材),生产直径121~150 mm削皮材。
(3)冶炼→模铸→3150 t快锻+1800 t精锻成材(简称3150+1800联合材)或1800 t精锻+3150 t快锻+1800 t精锻(简称1800+3150+1800联合材),生产直径151~300 mm削皮材。
(4)冶炼→模铸→3150 t快锻(简称3150直材),生产≥?301 mm削皮材。
1.2 设备参数
第二炼钢厂:主要设备有1座30 t非真空感应炉和1座30 t普通功率电弧炉、2座30 t LF炉、1座30 t VOD/VHD炉、1座30 t VD炉和5条台车式地坑浇铸线。根据锻造厂提锭要求,初炼钢水经过LF精炼炉、VD炉脱气后,可浇注成0.71、1.2、2.1 t或2.8、4、5 t或5.2、9 t或10~13 t可调锭型。
锻造厂:分为老线和新线。老线主要设备有1000 t精锻机、2000 t快锻机、3500 t快锻机。新线于2010年建立,主要设备有1800 t精锻机、3150 t快精锻机。加热设备有环型加热炉和室式加热炉,加热介质于2017年10月由水煤气改成天然气。
运输方式:带保温罩的汽车。
1.3 钢种的化学成分
1.4112钢种相当于国内9Cr18MoV钢种,可用于制造不锈钢切片、机械刃具以及剪切工具等材料。为了提高切削性能,多数用户要求钢中的硫质量分数按0.015%~0.030%控制。化学成分见表1。
2. 产品缺陷与质量检验
2.1 产品质量缺陷
新线发生的质量问题,主要有两种:
一种为钢锭掉尾,是指钢锭在锻造过程中,锭尾部分横向开裂而掉落,俗称掉尾,见图1。
一种为成品材探伤不合,伤波多数在20 dB以下,甚至底波消失,即伤波≥底波(F≥B)。在成品材部分断面的中心区域,有肉眼可见的孔洞,见图2。
2.2 低倍检验
取探伤不合材的低倍片做检验,见图3。低倍定性为中心孔洞。从低倍片可见,随着伤波的加重,低倍片上的中心缺陷越来越严重。图3(a)试片有肉眼可见较小的孔洞;图3(b)和(c)试片中心区域有非常明显的孔洞,与图2的缺陷一致。
2.3 高倍检验
切取探伤不合料的低倍试片(图4),将缺陷部分制成小试样进行高倍分析。图4(a)为伤波较轻的试片,横向切取,中心区域存在小孔洞;图4(b)为伤波较重的试片,纵向切取。在高倍下可观察到孔洞,孔洞附近均有碳化物存在,其中网状碳化物沿着碳化物发生开裂。
3. 分析与讨论
3.1 锻造过程中掉尾问题的分析
2015年在采用大锭型生产时,尾部脱落的比例占65.7%,影响了综合成材率[6]。
钢锭尾部异常脱落,主要是钢锭尾部产生内部应力,由内向外开裂。分析内部应力产生的原因是钢锭脱模时间过晚,脱模后钢锭尾部温度较低。当中心部位温度冷却到相变温度点(Ar1)以下时,如果继续冷却而且冷却速度太大时,就会在钢锭的中心部位产生很大的拉应力,会导致尾部脱落[6]。
通过进一步数据统计和研究分析,认为造成掉尾的第二个原因是加热炉待料温度低。由于此钢种为高碳马氏体钢,脱模时已获得了马氏体组织。由于钢锭预热不够,高温钢锭入加热炉后,由于炉温待料温度低,并没有对钢锭起到保温或升温的作用,反而使钢锭中心部温度进一步下降,加大了心部的应力。第三个原因是钢锭均温后,在低温段升温过程中,钢锭升温速度过快,由于此钢导热性不好,内外部应力进一步加大,形成更大的热应力和组织应力,导致内部横向开裂。锻造初期,在外力的作用下,钢锭或钢坯经加工变形后变成通到表面的裂口,严重时发生了掉尾问题,见图1。
3.2 探伤不合问题的分析
针对探伤不合,结合锭型、工艺路线,按成品材支数统计探伤合格率。老线采用0.71 t锭型和新线采用9.0 t锭型所生产的成品材,探伤合格率非常好;而新线采用1.2、2.1和5.2 t锭型所生产的成品材探伤合格率不好,尤其前两个锭型,探伤合格率更低,见表2。
因此,为查清影响探伤合格率的真正原因,结合高、低倍检验结果,同时收集现场的生产记录、影像等信息与品种工艺规程进行技术分析。通过比对,本次研究样本的高、低倍缺陷与以往探伤不合的缺陷相同,见图3、图4。
进一步调查、分析,具有这样的规律:
(1)钢锭保温时间过长。受生产组织、设备故障等因素影响,钢锭保温时间较工艺要求长。
(2)现场人员在保温时间的理解上存在差异。有人员认为,在钢锭出环形炉第三段进入第四段(保温段)时,开始保温时间的计时,而不是按炉温达到规程要求时开始计时。
(3)中间坯再烧时间过长。超规程要求时间。
(4)保温符合规程要求,但仍发生探伤不合的情况。整炉的均温和保温时间完全符合工艺规程的要求。当具备出炉生产条件时,先出炉的前半炉钢锭所产的材探伤全合格。但是由于小钢锭多,锻造时间长,导致后出炉的钢锭因在高温段滞留时间过长,所产材探伤合格率大幅降低。
(5)因设备故障,为保障生产的连续性,现场操作者通常按规程要求的下限温度加热保温。但是,由于故障解除具体时间无法确定,为提高生产效率,操作者又未按要求进行降温处理,人为导致了保温时间过长。
(6)钢锭装车、红送、装炉过程中存在意外故障,导致钢锭入炉温度低而发生掉尾问题。在锻造过程中,掉尾端的断面裂纹向内部延伸,导致探伤不合。
(7)加热介质由水煤汽改为天然气后,探伤不合的发生率比以前高。
3.3 其它因素的影响
为提高切削性能,要求钢中的硫质量分数按0.015%~0.030%控制。结合探伤情况来看,与锰硫比无明显对应关系,分别对比试验0.30% Mn和0.60% Mn,均有探伤不合的发生,发生不合的,均满足上文所述的共性问题。但为保证钢水脱氧、材料性能,锰含量也不适宜过低。
除锭型大小的差异、钢锭的保温时间、成材规格有所不同外,其它的工艺参数,如化学成分控制、钢锭加热出炉温度、中间坯的再烧温度、道次变形量在炉次间和各生产批次间的相差并不大。
通过上述讨论与分析,为解决探伤不合,调整方向应是钢锭保温时间及中间坯的再烧时间。
4. 工艺改进措施
由于加热介质的改变,天然气的热值比水煤汽的热值高,升温速度也比水煤气的升温速度快。如果仍按原来的工艺进行加热,对于易产生过热、导热性差、易形成穿孔的品种,不可避免地发生探伤不合。
通过上述分析与讨论,在采用新加热介质后,优化新线的生产工艺:
(1)为避免掉尾,继续采用高温红送,开辟绿色通道,首先保证此品种入炉,待料温度由原来的550~600 °C提高到650~700 °C。
(2)如果红送过程中发生意外,导致钢锭入炉温度低于常规温度,应调整加热炉待料温度(T1),使之与锭尾平均温度(T2)满足:T1=T2+(150±10) °C且待料温度不得超过700 °C。
(3)入炉均温后,低温段的升温速度控制≤50 °C/h。
(4)钢锭加热工艺的优化:保温温度1140~1160 °C,保温时间按4~8 h。
(5)中间坯加热工艺的优化:再烧温度1140~1160 °C,再烧时间依坯型按1.5~3 h控制。
(6)对于生产组织的要求:因设备故障或其他原因热停工不能按时出炉,调整为按下限保温。当总保温时间达到上限时,仍无法出炉生产时,降温到800~1000 °C;具备生产条件时升温且升温速度不限,料温达到工艺要求的保温温度后,保温时间按原工艺进行生产。降温到800~1000 °C且待料8 h仍无法生产时,按相关管理规定。
5. 效果验证
按上述优化方案,采用合适的锭型以保证加工比,共冶炼5炉钢。生产过程,加强红送的紧凑性。锻造过程中未发生掉尾问题,共生产125支材,探伤全都合格。自2017年10月以来,新线首次实现批次探伤合格率100%,见表3。
6. 结论
(1)加热介质的改变,对于高碳高合金比的特殊品种,应调整红送和加热工艺,避免发生掉尾、过热孔洞、探伤不合等缺陷。
(2)该钢种含较高Cr且含有Mo、V,均为易形成碳化物的元素。为避免过热孔洞的发生,除降低加热温度,还需关注保温时间,尤其在加热介质或炉窑发生改变后。
(3)该钢种含较高C、Cr且含有Mo、V,增加了钢锭的内应力。为避免因应力掉尾,应保证高温红送,且入炉待料温度控制在650~700 °C。
(4)此钢种为高碳高合金钢,为保证凝固质量,应严格控制浇注温度,并采用热周转包冶炼,防止因高温浇注产生锭偏、中心疏松等质量缺陷。
(5)质量是生产出来的。对于易发生探伤不合的品种,除了从专业角度科学分析、从工艺策划上加强技术保障外,在生产组织上,必须严肃地按工艺规程执行,并准确理解保温时间的概念。
(6)对于此钢种来说,锰含量并非引起探伤不合的影响因素,为节省成本,降低锰含量或低锰硫比是可行的。
(7)此钢种不适宜变冷锭。采用冷锭生产时,需要冶金工作者结合本文所述,进一步研究冷锭的加热工艺。
参考文献
[1]
霍育林,夏琴香,黎明,等. 轴类大锻件锻造工艺研究现状与质量检测方法. 现代机械,2008(增刊):98
[2]
郭会光,曲宗实. 我国大锻件制造业的发展. 大型铸锻件,2003,01(1):42doi: 10.3969/j.issn.1004-5635.2003.01.013
[3]
郭会光. 我国大型锻造的发展与提高. 机械工人(热加工). 2005(7): 14
[4]
陈再枝,蓝德年. 模具钢手册. 北京:冶金工业出版社,2002:1
[5]
中国机械工程学会塑性工程学会. 锻压手册, 北京: 机械工业出版社, 2008: 206
[6]
韩凤军,赵丹,唐亮. 1. 4112钢生产工艺研究. 大型铸锻件,2018(6):44
文章来源——金属世界
|